About the Experiment
State-of-the-art neutrino detectors are required to be very finely granulated in order to observe even low energy particles produced in neutrino interactions. A popular choice of technology are "scintillator" detectors. In these detectors particles produced in neutrino interactions produce light via a chemical process called scintillation that are then transported to photosensors via optical fibres. To achieve a fine granularity, state-of-the-art detectors are built of optically-separated miniature cubes which can be as small as 1cmˆ3. For example, T2K's recent upgrade of its ND280 detector is built from 2 million of such cubes with fibres carefully threaded through small holes within them in three directions. These detectors are highly performant, but are very challenging to build simply because of the challenges in aligning so many small holes across so many small cubes. Moreover, each of the cubes has to be individually manufactured.
The 3DET collaboration aims to make the mass production of large scintillator detectors much easier by 3D-printing them. 3DET has developed a method of simultaneously 3D printing with multiple materials (some for the scintillator, some for the opaque layer to keep cubes optically separated) to produce not individual small cubes, but a large "super cube" made of many optically separated "voxels". In their latest work, they also leave space for the insertion of the optical fibres in each voxel, making the detector manufacturing process extremely simple. The following figure shows the manufacturing stages of one voxel of a super cube: a) fabrication of an opaque cube wall; b) filling with the scintillator material; c) placing of the top surface; d) insertion of the fibres. The right figure shows a 3D printed supercube with fibres inserted under a UV light with the top layer removed to show the fibres inside each voxel.
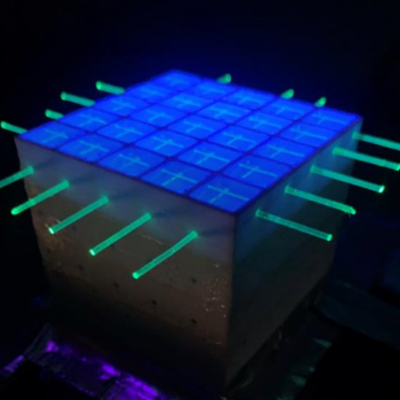
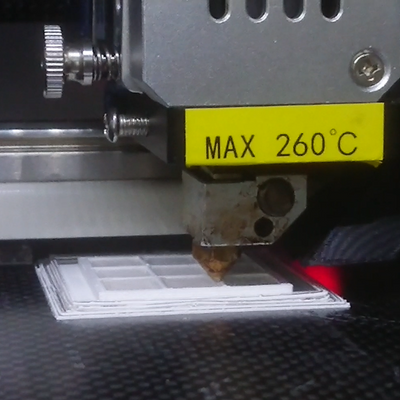